IIoT asset health monitoring and how it can help your plant
Plants are often a plural environment, with many brands integrated into one system. Can you have a plural IIoT (industrial internet of things) service that gives you accurate and timely monitoring? Read on!
If you look around your plant, I’m sure you’ll see more than one instrumentation brand. And even though standardization brings lots of benefits to end-users, you won’t find many examples of it.
So monitoring the health of your devices and processes can be a challenge in a plural environment with multiple brands. The lack of standardization in some protocols for reading diagnostics makes it hard to find a solution that fits all your instrumentation.
On the bright side, you can find IIoT-asset health monitoring systems that support multiple brands, and the number of devices they support expands with every update.
Let’s understand why health monitoring services are essential, and what you need to know before you set up an IIoT predictive service. Sound good?
What’s an asset health monitoring service?
Most field devices can provide a bunch of relevant health information. Even though few plants take advantage of this feature, it can improve plant operation and production performance.
Asset health monitoring has been around in automation for a while, so you can find plenty of software solutions on the market for it, such as Endress+Hauser’s FieldCare. However, the monitoring usually happens locally, with most cases using standalone solutions or an offline network with server and clients.
Sometimes, you find a company that allows remote access to the server, but it’s super rare. Most of the time, you get stuck with a slow connection.
I remember visiting a chemical plant years ago, working with the controller to access the server. Do you think we had high-speed internet? Nope. I was dismayed to find a dialup modem.
I’m sure some of you out there have never even seen one. Count yourselves lucky. Those of you who immediately heard that classic connection noise in your heads can confirm that it takes aaaaaaages. So yes, some older plants have remote access using PAM (plant asset management) solutions, but doing it this way is almost painful.
So how do IIoT systems work, and how are they better than PAM systems? Great question. Asset health monitoring is easier than ever, so let’s dive into the details.
Traditional asset health monitoring architecture
You need to understand how the traditional health monitoring works in order to see how IIoT health monitoring simplifies everything and brings many more benefits.
A standard health monitoring solution follows the five levels of the good old automation pyramid, as shown here:
In a standard health monitoring solution, this structure connects the field devices to the controller. You have an HMI (human-machine interface) to display the process information at the workstation, and then a PAM setup to access the field data.
In many cases, the PAM solutions access the field devices through the control system. Some customers like this setup just fine, and those who don’t would apply some parallel alternatives, such as gateways or WirelessHART networks.
You can also read and write data using a PAM system, but you risk a lot if you do something wrong that affects the control system. You could even cause an unscheduled shutdown - rare situation.
However, the IIoT concept has changed this structure a bit.
IIoT asset health monitoring architecture
Take the NOA (NAMUR open architecture), for example. It’s designed specifically to the control system, and its solid structure provides robust operation and high data availability for decades.
The central concept of NOA is to create an interface between the core process control and the M+O (monitoring and optimization) domain without risking plant safety. At the same time, this concept fits most solutions already running in plants without creating any interference.
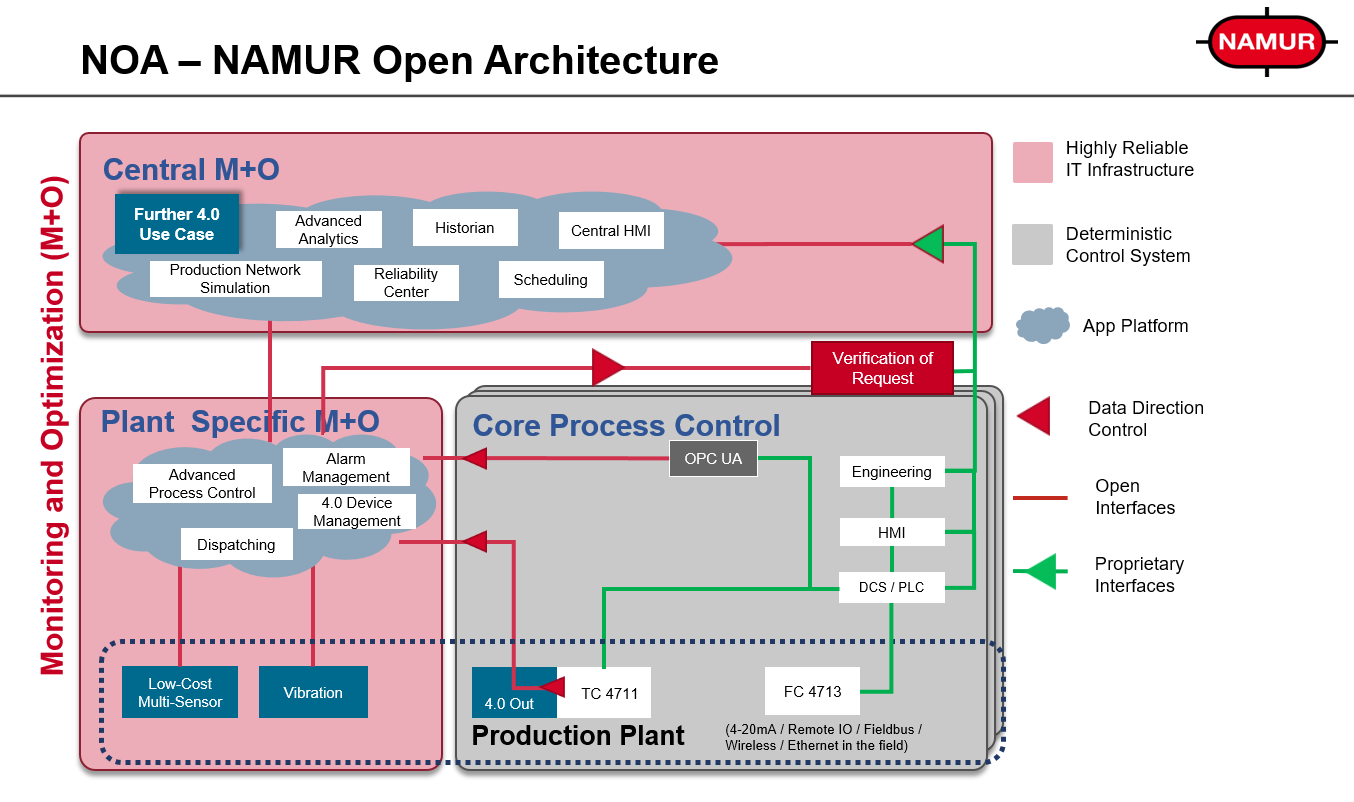
Unlike many in-plant solutions, most IIoT services follow the concept of one direction for data collection. While that sounds restrictive, it means you can access information and insights without interfering with the field devices.
Regarding the data collected from the core process control, you have the "NOA diode" between the devices and the M+O domain. It offers one-way communication from the core process control without remote interference from cloud services.
Third-party asset health services
In some protocols, the lack of standardization for reading field diagnostics makes health status updates from a single service challenging. So we have to find solutions where you can constantly update databases with the appropriate support for a variety of brands and their devices.
With most plants presenting plural environments, it’s essential to have IIoT services that provide the ability to integrate as many brands and devices as possible. For example, Netilion Health from Endress+Hauser starts out with an extensive list of devices supported in the service. And each update expands that list to cover more brands and models.

Health services that have constant database updates will allow you to pull whatever data you need from all your devices in the field. Of course, a plant that operates strictly with one brand can simplify service integration, but that’s a topic for another day.
If you learned something useful from this article, please share it with your colleagues on social media using the #Netilion tag.
Stay safe and have a good one!